近些年来,随着电子设备向轻薄化、小型化发展的趋势愈加明确,电子产品对PCB的高密度和高性能需求越来越突出。提高利用率、缩小板间距离,增加产量成为行业大势所趋,受到这些因素的影响,传统PCB机械分板法变得不切实际了,且成本增高,效益会变低。
激光切割技术的出现,为PCB分板带来了革命性的变化,其具有切割间隙小、精度高、热影响区小、无应力、切割边缘整齐光滑、操作灵活度高等明显优势,解决了传统加工方式弊端的同时,还能更好地满足PCB制造商在加工工艺和成本等方面的严苛需求。
应对这一需求,激光行业及自动化的技术先行者——马丁特尼尔以需求为目标,以开发市场为己任,长期专注于SMT行业。目前已打造出一支精锐的高端人才团队,不断进行技术创新,引领行业技术升级,积极进取不断创新,从而推出了激光切割机、电路板切割机等一系列高端激光切割设备。推动先进工业级激光器的国产化,为中国高端制造业注入新的活力和生机,在国内以至国际电子制造及装配领域中享有崇高的声誉。
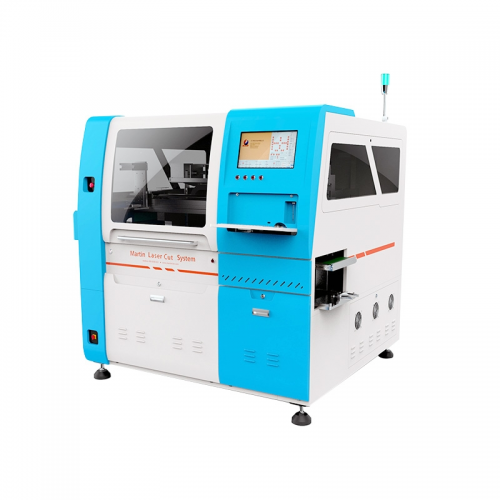
其中,马丁特尼尔新型激光切割设备——MicroCut1200系统一经推出便赢得业内专家高度认可,极大提升产能和良率,降低行业客户运营成本。功能强大的MicroCut1200系统凭借着优越的性能、高性价比、激光切割技术优势等决定性的因素,而在电子、医疗、精密配件等领域应用广泛。
这一系统采用了无接触切割工艺,明显提高对PCB分板的控制能力,确保精密、贵重元器件、焊锡连接敏感基板不会在分板过程中承受机械应力的冲击;系统还使用了计算机数据驱动加工,可以完全省去模具、工具费用,提高质量,实现极低的运行成本;此外,MicroCut1200系统更好地利用宝贵的拼版空间,切割缝及元器件之间的间距可以做到很小,元器件可以更紧靠边缘放置,电路板可以做得更小,更轻,常用于对切割质量要求较高的工件加工之中,为电子产品的升级精进创造了不可或缺的先决条件。
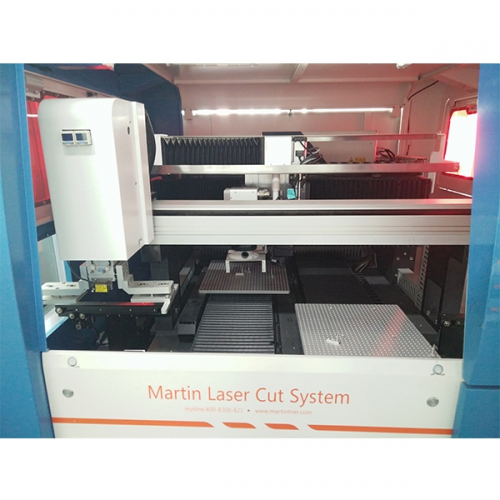
过去,传统的去除粉尘、碳化等缺陷往往都需要增加机械打磨或者抛光工序,还可能需要运用化学药水,既不环保,又格外耽误时间。MicroCut1200系统凭借独特的吸尘系统设计,可以全方位高效地收集加工时产生的粉尘,充分保护被加工产品的洁净度,还能避免对工作环境的污染,更使得器件长期处于清洁状态,不需要频繁维护。特有的专业加工程序,使得切割轮廓定位精准,无耗材,无残留。
当下,追溯系统作为一种可以对产品进行正向,逆向或不定向追踪的生产控制系统,目前已被广泛应用于各个行业中,适用于各种类型产品的生产和控制。MicroCut1200系统便设置了标准工业接口,可集成到MES系统中,支持操作数据的收集,机器分配,产品追溯、跟踪及配送监控,避免人工误贴、错贴、误印,实现了SMT生产线上产品的自动化、智能化的信息追溯,让制造商在激烈的竞争中随时随地更好地了解自身企业的发展与“健康状况”。
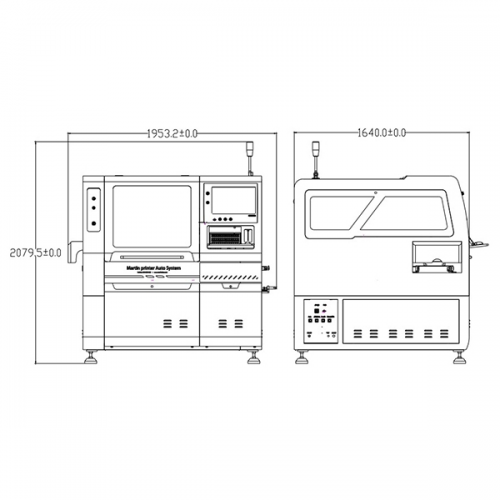
智能制造时代下,激光分板技术已经带来了诸多优势,PCB制造商已经将这项技术发挥到了极致。马丁特尼尔MicroCut1200系统的出现,无疑打开了更开阔的视野,充分满足了当下电子和汽车行业当前及未来的要求,凸显出公司自身的激光分板技术优势,既适用于以质量、效率、成本优势对传统机械加工技术进行更新换代,也能满足国际顶尖机构各种高端产品需求,已然成为尖端科技与精密制造的联结桥梁。